Quality control points of each process of photovoltaic modules
12/04/2022Quality control points of each process of photovoltaic modules
1. Preparation group quality control point
The main materials prepared by the preparation group are: battery, backplane, EVA, tin-coated tape, glass, aluminum frame, etc.
Appearance of the cell: The cell should not have cracks, splinters, or fragments (collapsed edges and corners). A single cell should not have obvious uneven color, and the cells of the same module should have the same color. Electrical performance: The electrical performance of each component must first require the same level of power, and then be matched according to the working current (IWORK) of the battery. The working current of the cells in the unified power module should be at the same level. If the same level of cells is missing, the one with higher power and current should be selected for patching.
Laser dicing: The diced cells not only meet the requirements of the drawings in size, but also the cutting depth is required to be within the range of 1/2-2/3 of the thickness of the cell when the scribed cells are observed under an optical microscope. And the cell has no edge chipping and cracks, and the cutting surface is visually smooth and bright.
TPT /EVA: When cutting TPT /EVA, it must be cut according to the size specified in the bill of materials. When encountering special materials, the modification of the size must be notified to the technology and process. In addition, there must be communication between each process. At the same time, the cutting size of the material must be measured and recorded every two hours.
Tin-coated tape: The cutting of the tin-coated tape should first be cut according to the size specified in the bill of materials. In fact, the size should be measured from time to time during the cutting process. The soaking time and baking time of the tin-coated tape are based on the process operation instructions specified as standard.
Glass: When glass is pulled from the warehouse to the workshop, the size of the glass must first be confirmed before use, and the size of the glass should also be sampled during the production process.
2. Belt quality control points
The first is to calibrate the temperature of the soldering iron tip and the heating table so that it must work within the process temperature range. Welding surface: The welding surface is smooth and bright, free of solder slag, dirt, high-point burrs, and white flux (the tip of the soldering iron must be replaced every 5 jobs and make a record). Welding effect: no virtual welding, desoldering, disconnection...
Soldering dislocation: The distance from the end of the front tinned tape to the edge of the cell is 3mm (±0.5mm) and the offset of the busbar is<0.5mm. Appearance inspection of the cell: no cracks, cracks, fragments (chipping and missing corners)......
3. String quality control points
The first is to calibrate the temperature of the soldering iron tip and the heating table so that it must work within the process temperature range. Welding surface: The welding surface is smooth and bright, free of solder slag and dirt.
Welding effect: Check that the front and back sides of the cell can not have virtual soldering, desoldering, disconnection... There must be no high points on the tin-coated tape, and burrs exist.
Welding misalignment: the offset of the tin strip on the front side of the two adjacent cells is ≤ 1mm, the offset of the tin strip on the back side is less than 1/2 of the bus line, and the distance between the two adjacent cells is 2 (±0.5mm ).
Appearance inspection of the battery sheet: no cracks, cracks, fragments (collapsed edges and corners)...
4. Typesetting quality control points
When swinging, the distance between the head of the battery string and the edge of the glass, the distance between the tail and the edge of the glass, and the distance between the battery string and the edge of the glass on both sides must meet the design requirements of the drawing, the welding of the busbar should meet the requirements of the drawing, and the lead wires must be bent at a certain angle. Moreover, the leads should not be deformed. The fixation of the high-temperature adhesive tape must be attached according to the design of the drawing, and none of them can be missing.
When laying insulating TPT and TPT, the alignment point must be at the bend of the lead.
Check that no debris (solder slag, hair, tpt wire) is allowed in the middle plate.
5. Lamination quality control points
The parameter settings of the laminator must meet the requirements of the process document. The temperature point inspection of the laminator and the actual temperature are within ±2, which is qualified. The corresponding process parameters must be adjusted when the material (EVA) is replaced.
For the high temperature cloth after each lamination, the EVA glue remaining on the silicone plate must be cleaned up in time.
Daily temperature inspections and cross-linking experiments must be done, and the standards must be checked to see if they are within the normal range. The EL test and appearance inspection of the modules are in accordance with the inspection standards of each company's "Crystalline Silicon Solar Module Inspection Specifications".
6. Assembly quality control points
The assembly quality control points are mainly as follows: after the frame assembly machine completes the frame assembly, it is necessary to pay attention to whether the B side of the frame is scratched from time to time. After the assembly is completed, the gap between the long frame and the short frame cannot exceed 0.5mm. For the components after the frame is assembled, the size of the diagonal should be measured regularly and recorded.
7. Test quality control points
Test under standard test environment: STC condition: 1000w/m², AM1.5, temperature 25℃±2℃.
The calibration procedure must be operated in strict accordance with the operation instructions, the component labels shall meet the design requirements, the handwriting shall be clear, and the printing shall be clean.
8. Packaging quality control points
The packaging control points are mainly manifested in: the phenomenon of lack of glue on the back of the module must be very sensitive, and the front squeegee and cleaning must be done so that no swag adheres to the glass.
The appearance of the carton should be clean with no visible scratches. The product model, quantity, and manufacturer's information are clearly visible.
The outer box should have fragile or non-pressure labels, and the labels should be firmly, neatly and beautifully pasted. After packing, the distance between the packing strip and the edge of the box is symmetrical and beautiful.
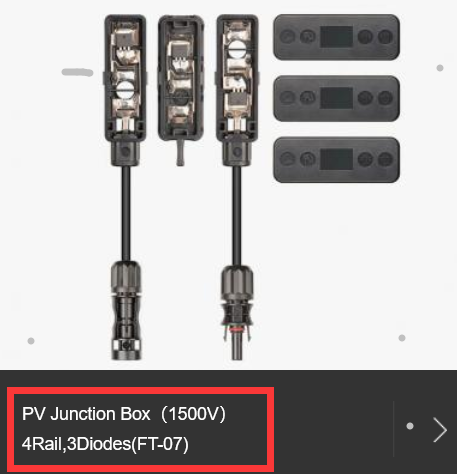
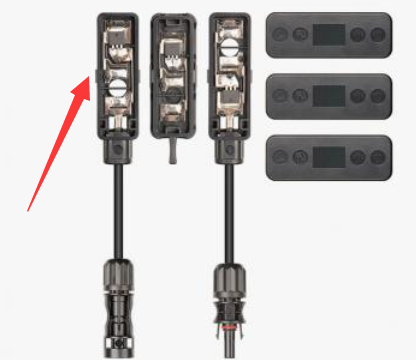
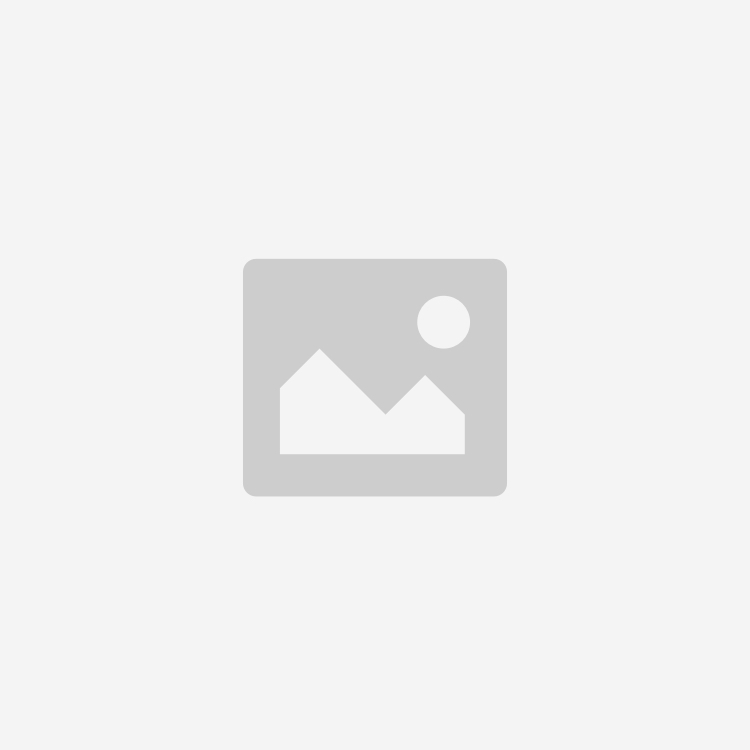
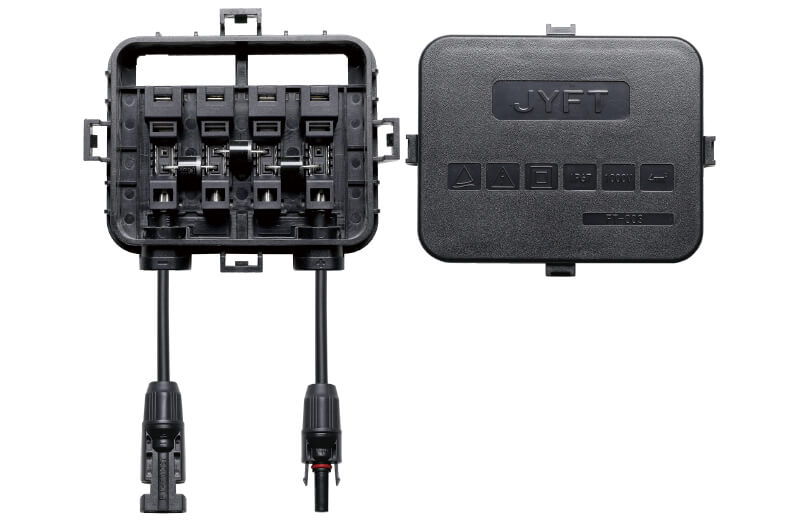
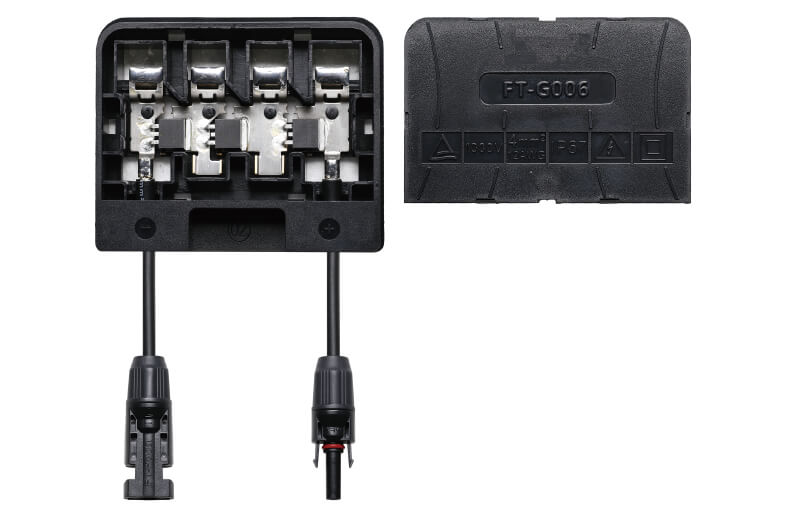
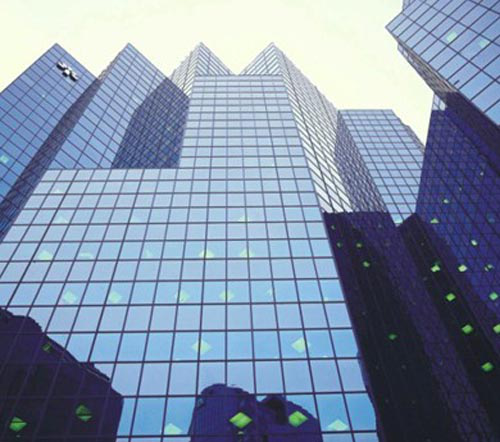